In today's dynamic business environment, manufacturing companies face numerous challenges, with cost fluctuations among the most significant. Cost fluctuations can arise from various factors, including raw material prices, labor expenses, transportation costs, and economic conditions. Understanding the impact of these fluctuations on manufacturing is crucial for companies to maintain profitability and sustain long-term growth.
This blog post article delves into the intricacies of cost fluctuations, their implications for the
manufacturing sector, and where you can start reducing operating costs at your facility.
Understanding Manufacturing Costs
Manufacturing costs encompass a broad spectrum of expenditures associated with producing goods. They typically include raw material costs, labor expenses, overhead costs, and indirect expenses. These costs vary depending on the industry, production processes, and market dynamics. Therefore, manufacturers must clearly understand their cost structure to analyze and manage fluctuations effectively.
Factors Influencing Cost Fluctuations
- Raw Material Prices: Raw material costs substantially impact manufacturing expenses. Fluctuations in commodity prices, supply chain disruptions, and geopolitical factors can all contribute to volatile raw material costs.
- Labor Expenses: Labor costs play a vital role in manufacturing operations. Factors such as minimum wage laws, labor market conditions, and changes in employee benefits can lead to cost fluctuations in this area.
- Transportation Costs: Manufacturing companies heavily rely on transportation to move raw materials, components, and finished goods. Fuel prices, shipping rates, and regulatory changes can cause transportation costs to fluctuate significantly.
- Economic Conditions: The overall economic climate greatly influences manufacturing costs. Factors like inflation, exchange rates, interest rates, and market demand can create cost fluctuations that impact manufacturers' financial performance.
Impact of Fluctuations on Manufacturers' Bottom Line
Fluctuations in costs can have profound effects on a manufacturer's bottom line. When costs rise unexpectedly, profit margins can shrink, making it challenging for businesses to remain competitive. Conversely, cost reductions can improve profitability, allowing manufacturers to invest in innovation, expansion, or employee development. Manufacturers must closely monitor cost fluctuations and adapt their strategies to maintain financial stability and sustainable growth.
Strategies to Manage Cost Fluctuations
- Risk Assessment and Planning: Manufacturers should conduct thorough risk assessments to identify potential cost fluctuations. By anticipating and planning for these changes, companies can implement proactive strategies to mitigate their impact.
- Supplier Relationships and Negotiations: Building solid relationships with suppliers and negotiating favorable contracts can help manufacturers stabilize costs. Long-term partnerships, volume commitments, and supplier diversification strategies can offer stability and reduce vulnerability to price fluctuations.
- Lean Manufacturing Practices: Implementing lean manufacturing principles can optimize production processes, minimize waste, and improve cost efficiency. Continuous process improvement and waste reduction initiatives can help manufacturers navigate cost fluctuations and maintain competitiveness.
Using Airend Overhaul or Rerates to Reduce Costs
Since
air compressors are considered the fourth utility for a plant operation, finding ways to improve efficiency and reduce operating costs is an excellent place to start to best prepare your organization for cost fluctuations.
Airend Overhaul Benefits
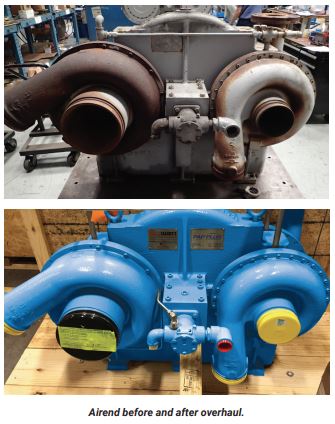
An
airend overhaul in a centrifugal air compressor can provide several benefits, including improving performance, increased reliability, longer life span, and reduced energy consumption. For example, overhauling the airend can improve compressor performance by restoring it to its original operating conditions. This will increase the life of moving parts within the airend core, restore vibration levels to OEM standards, and provide an additional warranty. In addition, scheduling regular overhauls over the life of your compressor helps prevent mechanical issues and significant damage to other components, reducing the need for more costly repairs or replacements.
Energy efficiency has become crucial across all industries, and a worn airend can lead to increased energy consumption, resulting in higher overall operating costs. Operators that select an airend overhaul can expect lower energy requirements and higher system efficiency.
Airend Rerates Benefits
An airend rerate involves changing some of the compressor’s internal components without replacing the entire skid assembly. Benefits of a rerate include increasing performance, higher energy efficiency, and improved reliability. A rerate can help reduce energy consumption and operating costs by upgrading the airend components, such as impellers and diffusers, and increase the compressor's capacity, allowing it to produce more compressed air in less time. Minor adjustments can also make a significant impact on discharge pressure and also increase design flow capacity.
Rerating an airend offers the ability to increase performance by 30-50%. While centrifugal compressors are able to operate within a specific range, their capabilities are limited by the conditions they were designed for when the compressor was initially manufactured.
Consider Airend Derates for Certain Applications
Sometimes a compressor’s initial design was too large for its intended application, consuming more energy than needed and blowing off the excess capacity. In this situation, an airend derate can be a great option as it will adjust the capacity and discharge pressure to save power usage, reducing the manufacturer’s utility costs.