The Role of Compressed Air in the Fermentation Industry
Compressed air is essential to
pharmaceutical and biological fermentation processes, providing a clean, controlled, and reliable source of air for various critical applications, including:
- Aeration for Microbial Growth: Supplies oxygen-rich air to fermenters, crucial for the growth of aerobic microorganisms and the production of metabolites like antibiotics, enzymes, and bioethanol.
- Temperature Control: Powers pneumatic control valves in cooling systems to regulate fermenter temperature.
- Cleaning-In-Place (CIP): Facilitates the cleaning and sterilization of fermentation tanks and pipelines through automated cleaning systems.
- Agitation and Mixing: Delivers air to create bubbles or streams, ensuring uniform mixing of culture media to enhance fermentation efficiency.
- Moisture and Sterility Control: Compressed air is dried and filtered to remove moisture and contaminants, maintaining sterile and controlled fermentation environments.
- Pneumatic Systems: Drives automated valves and instruments in fermentation systems for precise process control.
Air quality is critical in pharmaceutical and biological fermentation. Even minor contamination from oil, bacteria, microorganisms, or particulates can compromise product integrity. To maintain the highest purity standards, oil-free air compressors must comply with
ISO 8573-1 Class 0 oil-free air quality, providing clean, reliable, and uncontaminated air.
Compressed Air Demands for the Fermentation Process
The required air pressure for fermentation processes depends on the specific application and system design, typically ranging from 1.5 to 3.5 bar(G) (22 to 50 psi(G)).
Several factors influence air pressure requirements, including production scale, microorganism type, and system design. For air sparging or agitation, pressures generally range from 1.5 to 2.5 bar(G) (22 to 36 psi(G)) to generate fine bubbles for efficient mixing. Larger fermenters or aerobic microorganisms may require higher pressures to ensure consistent air and oxygen supply throughout the fermentation medium. To achieve optimal oxygen transfer rates in high-demand fermentations, such as antibiotics or bioethanol production, air pressure and flow must be precisely controlled.
In the fermentation industry, air consumption is often measured in terms of airflow per unit volume of the fermenter, commonly referred to as Vessel Volumes per Minute (VVM). This metric represents the air supplied per minute relative to the fermenter’s total volume. Different microorganisms may require varying air volume rates, with a typical guideline of 0.5 to 1.5 VVM for fermentation processes. For large-scale fermenters, particularly in pharmaceutical and biological fermentation, vessel volumes of approximately 12,000 liters are common. For a system using 10 such vessels, the total compressed air demand would be approximately 120,000 L/min or 4,500 cfm at 2.5 bar(G).
Efficient Performance with Centrifugal Compressors
The most common system configuration for fermentation applications currently involves supplying air through a main pipeline, with a flow control valve installed in front of each fermenter to regulate the airflow. Each fermenter has a flow control valve, which adjusts the amount of compressed air entering the fermenter. The compressor automatically adjusts its discharge capacity based on the pressure signal from the main pipeline network.
The compressed air demand usually is very stable in terms of both pressure and flow rate. Once the airflow demand exceeds 30 m
3/min or 1,000 cfm, the best practice is to use
centrifugal compressors to benefit from higher energy efficiency and the highest uptime.
The two-stage integral geared centrifugal compressor (IGC) is highly efficient at delivering large airflows at lower discharge pressures, such as 2.5 bar(G) or 40 psi(G), while meeting ISO 8573-1 Class 0 oil-free air quality standards. FS-Elliott compressors are designed with low-pressure ratio stages and optimized for two-stage applications, making them ideal for the pharmaceutical and biological fermentation industries. FS-Elliott’s reliable Polaris compressors feature our patented Regulus Control Panels, which support integrated compressor control (ICC) for seamless compressor network integration. This system maximizes energy efficiency through advanced guide vane throttling and load sharing.
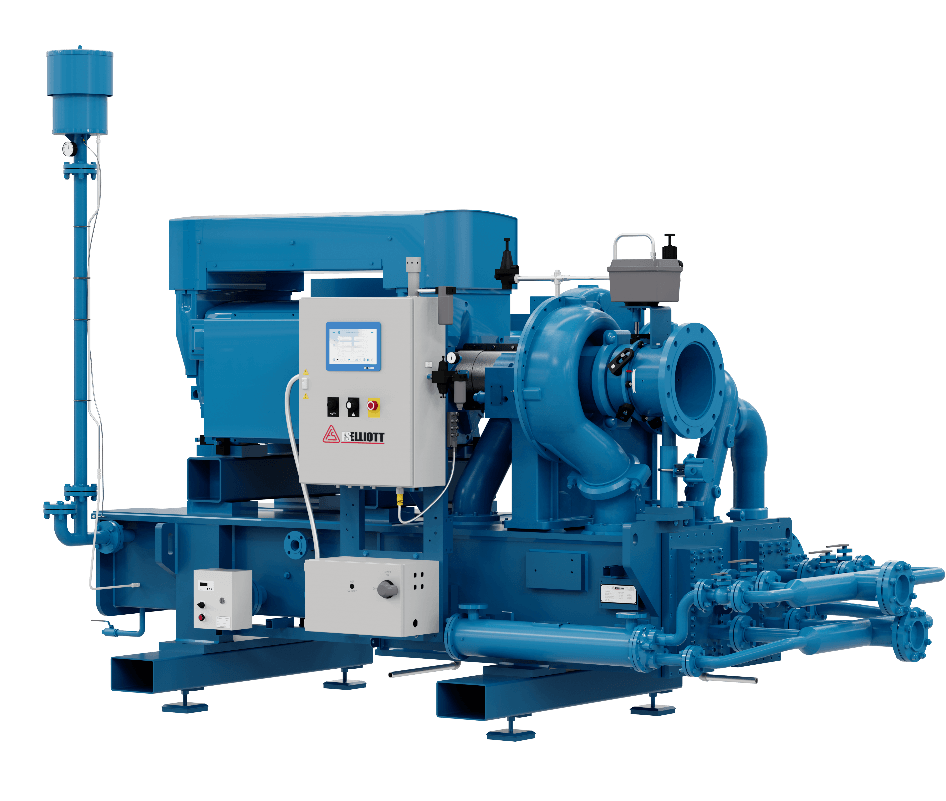
For example, the FS-Elliott two-stage
P500 compressor, with optimized aero stages, can deliver 4,620 cfm at 40 psi(G) in specific scenarios, helping save 13% of lifecycle costs over a 12-year operational period compared to other compressors.
Maximizing Efficiency in Fermentation with the Right Compressed Air Solutions
In the pharmaceutical and biological fermentation industries, the role of compressed air cannot be overstated. From providing oxygen for microbial growth to supporting critical processes like agitation, temperature control, and cleaning, reliable and efficient air systems ensure optimal fermentation outcomes. Businesses can achieve superior energy efficiency, lower operating costs, and maintain the highest air quality standards by selecting the right centrifugal compressors, such as FS-Elliott's two-stage Polaris compressors. These systems are designed to meet the demanding requirements of large-scale fermentation, offering the reliability and performance needed to produce antibiotics, bioethanol, and other essential bioproducts.
Ready to Optimize Your Fermentation Processes?
Contact us today to learn more about how our FS-Elliott centrifugal compressors can help improve efficiency, reduce costs, and ensure the highest quality air for your applications.